CNC machining refers to computer numerical control machining, where computer programming controls the machining tools. It offers advantages such as stable machining quality, high precision, and the ability to process complex shapes. However, in actual machining, human factors and operational experience significantly impact the machining quality. Below is a summary of twelve valuable experiences from someone with ten years of CNC machining experience.
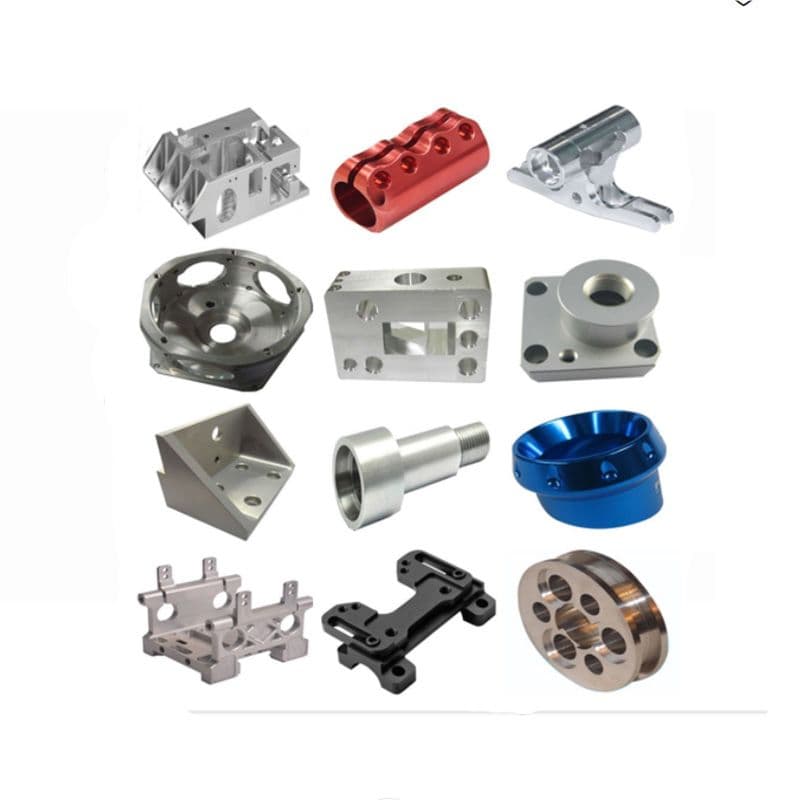
1. Machining Process Division Methods
- Tool Concentration Method: Divide the process according to the tools used. Use the same tool to complete all accessible parts of the workpiece, and then switch to another tool. This method reduces the number of tool changes, shortens idle time, and minimizes positioning errors.
- Process Division by Machining Location: For parts with many features, divide the machining into internal shapes, external shapes, curved surfaces, or flat surfaces based on structural characteristics. Typically, flat surfaces and reference surfaces are machined first, followed by holes. Simple geometric shapes are processed before complex ones; lower precision areas are processed before higher precision areas.
- Process Division by Roughing and Finishing: For parts prone to deformation, rough machining may require reshaping. Thus, rough and finish machining operations are usually separated. When dividing processes, consider the part structure, machinability, machine tool capability, machining content, number of setups, and production organization to determine whether centralized or decentralized processes should be used.
2. Principles for Arranging the Machining Sequence
The machining sequence should be determined based on the part's structure, raw material condition, and positioning/clamping requirements, with a focus on preserving the workpiece's rigidity. Follow these principles:
- The previous operation should not affect the positioning and clamping of the subsequent operation, even when interspersing operations on general-purpose machines.
- Begin with internal shapes and cavities, then move to external shapes.
- Operations that use the same positioning and clamping methods or the same tool should be carried out consecutively to reduce repeated repositioning, tool changes, and fixture adjustments.
- For multiple operations in the same setup, prioritize those that cause minimal damage to the workpiece's rigidity.
3. Key Points for Determining Workpiece Clamping Method
When determining the positioning and clamping scheme, ensure the following:
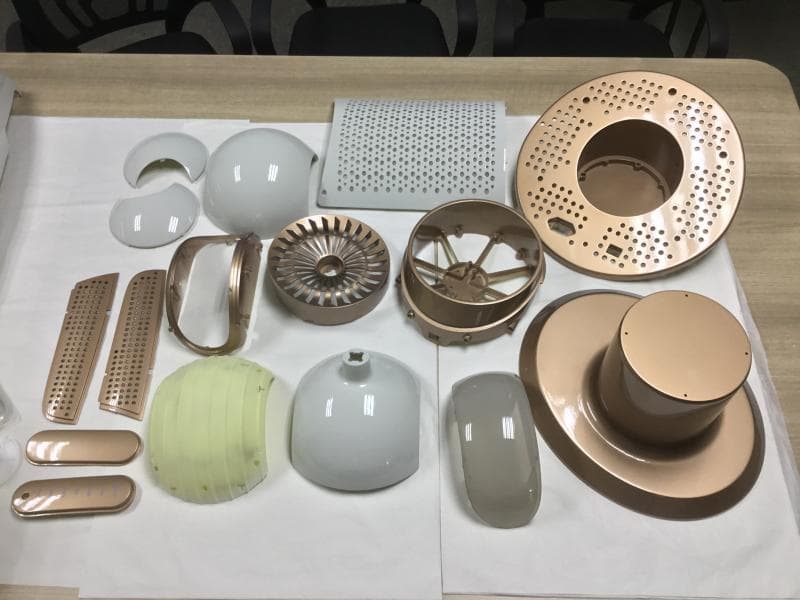
- Ensure that the design, process, and programming references are unified.
- Minimize the number of clamping setups, aiming to machine all surfaces in a single setup.
- Avoid using manual adjustment methods that occupy machine time.
- Fixtures should be clear, and the positioning and clamping mechanism should not interfere with the tool path. Use vices or additional bottom plates and screws to clamp if necessary.
4. Determining the Tooling Point and its Relationship to the Workpiece Coordinate System
- Tooling Point Determination Principle: The tooling point can be set on the workpiece but must be a reference position or a part that has been finish-machined. In the first operation, set the tooling point relative to a fixed reference on the workpiece, such as the machine table or fixture. The principle is to select an easily aligned position that simplifies programming, minimizes tooling errors, and facilitates inspection during machining.
- Workpiece Coordinate System vs. Programming Coordinate System: The workpiece coordinate system origin is determined by the operator during clamping and tooling. It reflects the distance relationship between the workpiece and the machine tool zero point and generally remains fixed once set. The workpiece coordinate system and the programming coordinate system must be unified.
5. Choosing the Tool Path
The tool path is crucial for machining accuracy and surface quality. When selecting the tool path, focus on:
- Ensuring the part meets the machining accuracy requirements.
- Simplifying numerical calculations and reducing programming workload.
- Seeking the shortest machining path to reduce idle time and increase machining efficiency.
- Reducing the number of program segments.
- Ensuring that the roughness of the final part profile meets surface finish requirements. The final tool pass should be used for continuous finishing.
- Planning the tool approach and retraction routes rationally to avoid tool stops at the part contour or vertical cuts that could damage the workpiece.
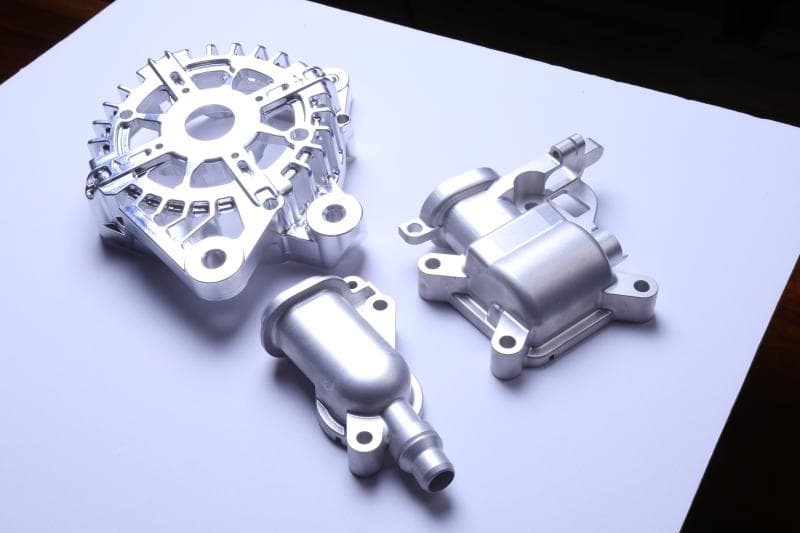
6. Machining Process Monitoring and Adjustment Methods
- Machining Process Monitoring: During rough machining, focus on quickly removing excess material. Monitor cutting load changes using load charts and adjust cutting parameters accordingly.
- Cutting Sound Monitoring: During normal cutting, the sound should be stable, continuous, and smooth, with steady machine motion. If the sound changes, or there is impact or vibration, adjust the cutting parameters. If the issue persists, pause to check the tool and workpiece.
- Finishing Process Monitoring: Ensure dimensional accuracy and surface quality. Watch out for chip accumulation, overcutting at corners, and tool engagement issues. Adjust the coolant spray position, observe the surface quality, and check the program if necessary. Ensure the tool is positioned correctly when stopping to avoid tool marks.
- Tool Monitoring: Monitor tool wear or damage through sound, cutting time, pause checks, and surface analysis. Take action to address any issues.
7. Tool Selection and Cutting Parameters
- Tool Selection: For face milling, use non-resharpened hard carbide end mills or vertical mills. For rough milling, the recommended tool width is 60%-75% of the tool diameter. Use end mills with inserted carbide tips for machining bosses, grooves, and openings. Ball mills and round mills are used for machining curved surfaces and variable-angle profiles, with ball mills typically used for semi-finishing and finishing. Round mills with carbide inserts are used for roughing.
- Cutting Parameters: Cutting parameters include cutting depth, spindle speed, and feed rate. The general principle is to minimize cutting depth and maximize feed rates.
- Tool Materials Classification: Tools can be classified into standard high-speed steel (HSS), coated tools (e.g., titanium-coated), and alloy tools (e.g., tungsten carbide, boron nitride).
8. Purpose and Content of the Machining Program Sheet
- Purpose: The machining program sheet is a CNC machining process document that operators must follow. It details the program contents, clamping and positioning methods, tool selection, and considerations.
- Content: It includes drawing and programming file names, workpiece names, clamping sketches, program names, tools used, maximum cutting depth, machining characteristics, and theoretical machining time.
9. Preparation Work Before CNC Programming
Before programming, ensure an understanding of the clamping method, blank size, workpiece material, and tool availability. This helps avoid modifications to the program due to tool-related issues.
10. Setting the Safe Height in Programming
The safe height is generally set above the highest island surface or the highest point in the program’s reference. This ensures no tool collisions occur.
11. Post-Processing of Tool Paths
Different machine tools recognize different address codes and NC program formats. Therefore, select the correct post-processing format based on the machine tool used to ensure the program can run correctly.
12. Introduction to DNC Communication
Programs can be transferred via CNC or DNC methods. In CNC, the program is delivered to the machine tool's storage via a media device and is retrieved for machining. When the program is large, DNC is used, where the machine tool reads the program directly from the control computer (processing while receiving), overcoming storage capacity limitations.